Kerry Pianoforte, Editor 10.13.20
Company Profile: Blocksil
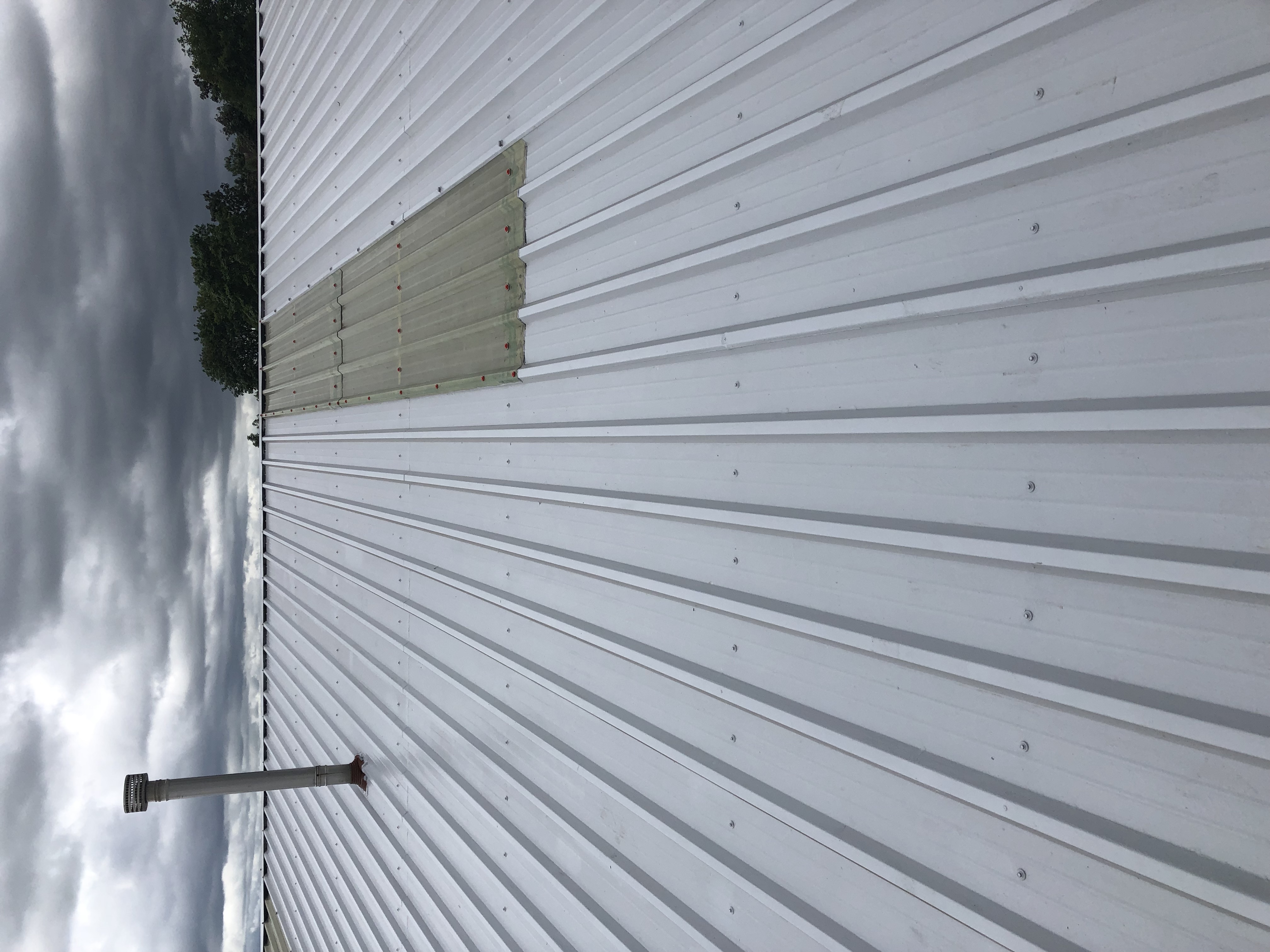
Blocksil has invented and developed a Graphene enhanced corrosion resistant coating with inherent anti-graffiti and easy clean properties.
Coatings World: Who or what is Blocksil?
Blocksil: Blocksil’s very existence is centered around coatings innovation and development. In recent years we have been working on improving the somewhat moribund roof coating market and, with our UK distributor (Alltimes Coatings, Gloucestershire, England), have taken the UK market by storm. Our roof coating uses the latest generation hybrid chemistry and is significantly quicker to apply than other, older technology systems. This helps reduce time on the roof and cost for all concerned. As part of our ongoing ethos of product development, we came up with the idea of adding Graphene to our roof coating to further enhance its corrosion resistant properties.
CW: What is the connection between roof coatings and corrosion resistance?
Blocksil: Corrosion of steel has been a problem for as long as steel has been used for structural purposes. The reduction in the steel’s physical state clearly has all manner of safety and performance issues not to mention cost. Some reports suggest that steel corrosion costs the global economy around £2 trillion per year1, which equates to 3% of global GDP. The use of coatings or paints to protect the steel likewise has a long history with global sales of anti-corrosion coatings in the region of £18 billion per year2. And a steel roof is like any other steel structure – it will corrode if not protected. When new, the steel is galvanised and overcoated with a functional decorative coating. Over time corrosion occurs at the cut edges of the steel sheets and also through the coating which leads to galvanizing failure.
Coating development tends to be gradual with incremental improvements in the base resins or the additives, with very little brand new happening. So by bringing in a radically new steel roof coating we effectively bring a radically new corrosion resistant coating to market.
CW: You mentioned Graphene - what is it?
Blocksil:Graphene was first isolated in 2004 at The University of Manchester, England. They used sticky tape to remove single layers from the surface of graphite and deposit them onto a silicon wafer. The isolation of Graphene was a breakthrough which ultimately won the 2010 Nobel Prize for Physics.
In its purest form Graphene has a molecular structure comprising of a single layer of Carbon atoms bonded in a hexagonal structure. Graphene possesses an unsurpassed combination of mechanical, electrical, and thermal properties. The Graphene used in Blocksil’s corrosion resistant coating is manufactured using a synthetic, bottom up process that is repeatable, proven and almost completely free of Graphitic impurities, Graphene Oxide or transition metals.
Our Graphene manufacturer and supplier, Applied Graphene Materials (AGM), UK, was founded by Professor Karl Coleman in 2010, with its operations and processes based on technology that he initially developed at Durham University, England. The creation of their Graphene is through a proprietary, patented process.
Andy Gent, Commercial Director at AGM, has worked with Blocksil from the beginning of this project and comments “Blocksil’s idea to use our Graphene within their corrosion resistant roof coating has taken everyone forward in terms of coating technology”.
CW: How does Graphene work in the coating?
Blocksil: The number of atomic layers varies but our Graphene typically has a 1 to 10 nanometre thickness with 1 to 15 microns lateral diameter, resulting in aspect ratios up to 1:1000.
To put this into perspective, the surface area of ten grams will cover a soccer pitch.
This large surface area provides an exceptionally long and tortuous path for any corrosive liquid to work its way through a coating.
Introducing the Graphene into the roof coating was and is a complex process as it cannot just be poured into the mix. The detail of the process is confidential but we can say that there had to be some work on pigmentation. Graphene is Carbon which is black of course. And as soon as one changes one constituent another needs tweaking. But it is here now and all can benefit from the enhanced performance.
CW: What benefits does the Graphene addition give the client?
Blocksil: Tested to ISO 9227 – Neutral Salt Spray, with testing in continuous 5% Sodium Chloride solution at 35oC, our Graphene enhanced coating has taken us past 11,800 hours! To put this into recognizable terms – for a roof we’re giving a 30 year product warranty. And in the automotive industry, coatings tend to be acceptable with up to 1,000 hours.
For more information on how well our Graphene enhanced coating works, Alltimes Coatings have created a highly professional online CPD (Continuous Professional Development) presentation which explains in greater detail just how the Graphene Enhanced Top Coat benefits steel surfaces. Entitled “Rust Never Sleeps”, this CPD is available via Alltimes Coatings (www.alltimescoatings.com).
CW: Do the coating applicators and contractors benefit from having a Graphene coating?
Blocksil: They certainly do. The coating is solvent, isocyanate and VOC free, and is applied as a single coat once the surface has been prepared. Because of its impressive spread rate, contractors can cover much larger surface areas than before and its stop / start technology also means the coating can be applied in stages without any time restrictions. This gives contractors a new level of freedom and flexibility and no adhesion problems with day edges and cut ins.
For elevated jobs scaffolding is needed for less time and safety is greatly improved with operatives spending less time working at height. In addition the coating does not need ‘hazardous storage’, which makes onsite logistics of handling and storage easy.
CW: Is the Blocksil Graphene enhanced coating available worldwide?
Blocksil: At present we’re just supplying the UK though we’re getting interest in the USA through our partner Marc Zirkle, who heads up Blocksil USA. We successfully carried out some coating trials last year in north east Georgia at an engineering works near the Tallulah River.
To date the Graphene Enhanced Top Coat has been approved for use by Avanti Communications, a multinational telecommunications company who operate satellites and the ground station dishes. These dishes are located around the world in often remote and corrosive sites.
The coating is also being rolled out on to communication masts for private and state owned use. These masts tend to be situated on the top of high ground such as mountains and suffer from flexing and high wind flow, both of which seem to increase corrosion levels.
Our next step is to start working with other infrastructure providers such as the railway networks. This is in addition to all the hundreds of steel roofs that have benefited.
CW: So where else can Graphene be used within the coating industry?
Blocksil: Blocksil is certainly working on incorporating it into other coatings, paints and treatments to take advantage of the enhanced corrosion resistance offered.
For example, we’re incorporating Graphene into a primer for use below the Top Coat. Simple you would think? Not quite as we’re also trying to take out all the solvent so we can offer clients a completely solvent free corrosion resistant coating system. This will give obvious benefits to the applicators and the environment.
And we’re working on developing the Top Coat still further to take advantage of some new polymer chemistry we’ve developed with one of our toll manufacturers.
CW: Are you looking at any other coating developments?
Blocksil: Yes, we’d like to make use of our knowledge of infrared reflectance coatings.
The idea is for a coating that reduces the amount of infra-red radiation absorbed by the coating, thereby reducing the amount of heat passed through it. There are clear benefits to be had, with reduced energy usage for air conditioning being one. This modification to the coating will add nothing to the weight or colour of the coating as we will be modifying the pigments and additives already in use.
CW: How will this work?
Blocksil: It is well known that a white or light coloured surface remains cooler than a black, or darker surface thanks to the interaction of the coating with the infra-red radiation emitted by the Sun. As infra-red radiation accounts for approximately 50% of the total energy of solar radiation, reducing the amount absorbed by the coating is clearly beneficial. By modifying the pigments and additives within the coating, Blocksil will be able to improve the Total Solar Reflectance (TSR) of the coating, even with darker colours.
Depending on the coating colour and the levels of brightness, laboratory tests suggest a temperature reduction of between 8.7oC and 14.7oC, with an improvement in the TSR of between 50% and 32%. An additional benefit of having an improved TSR is an enhanced lifespan of the coating. The reduced surface temperature will reduce any thermal degradation and temperature differences between day and night, direct sunlight and shadowed areas. This in turn would lead to reduced thermal warping and stress.
CW: How would you summarise Blocksil’s position?
Blocksil: Blocksil will continue our efforts to bring the very latest ideas and technology to the coating industry. Chris Knowles, Chief Technical Officer at Blocksil comments that “we believe there are opportunities for developing and cross benefitting different industries’ coatings away from older, less efficient coatings and we’re certainly well placed to help that happen”.
References:
1 National Association of Corrosion Engineers
2 Allied Market Research
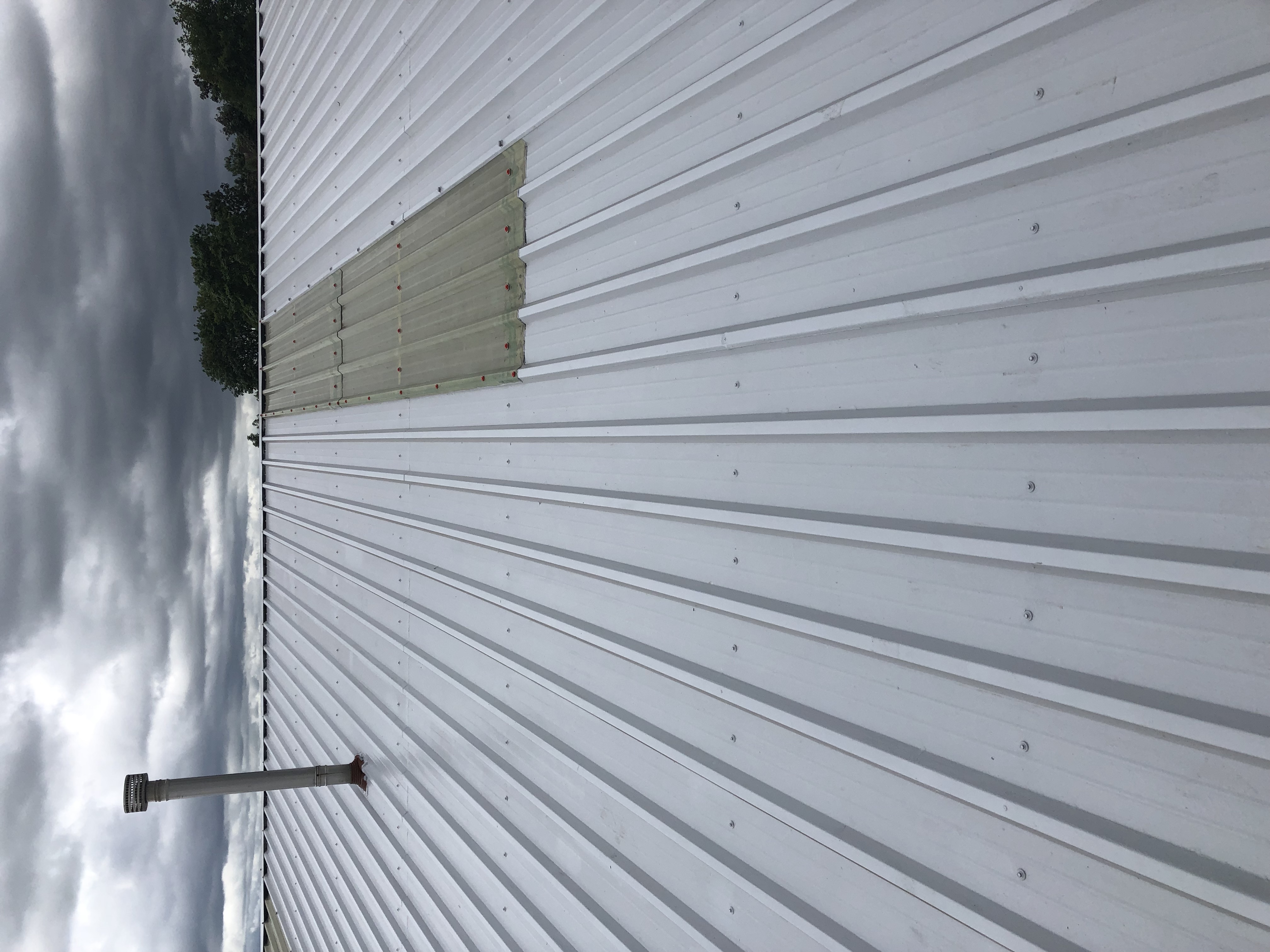
Blocksil has invented and developed a Graphene enhanced corrosion resistant coating with inherent anti-graffiti and easy clean properties.
Coatings World: Who or what is Blocksil?
Blocksil: Blocksil’s very existence is centered around coatings innovation and development. In recent years we have been working on improving the somewhat moribund roof coating market and, with our UK distributor (Alltimes Coatings, Gloucestershire, England), have taken the UK market by storm. Our roof coating uses the latest generation hybrid chemistry and is significantly quicker to apply than other, older technology systems. This helps reduce time on the roof and cost for all concerned. As part of our ongoing ethos of product development, we came up with the idea of adding Graphene to our roof coating to further enhance its corrosion resistant properties.
CW: What is the connection between roof coatings and corrosion resistance?
Blocksil: Corrosion of steel has been a problem for as long as steel has been used for structural purposes. The reduction in the steel’s physical state clearly has all manner of safety and performance issues not to mention cost. Some reports suggest that steel corrosion costs the global economy around £2 trillion per year1, which equates to 3% of global GDP. The use of coatings or paints to protect the steel likewise has a long history with global sales of anti-corrosion coatings in the region of £18 billion per year2. And a steel roof is like any other steel structure – it will corrode if not protected. When new, the steel is galvanised and overcoated with a functional decorative coating. Over time corrosion occurs at the cut edges of the steel sheets and also through the coating which leads to galvanizing failure.
Coating development tends to be gradual with incremental improvements in the base resins or the additives, with very little brand new happening. So by bringing in a radically new steel roof coating we effectively bring a radically new corrosion resistant coating to market.
CW: You mentioned Graphene - what is it?
Blocksil:Graphene was first isolated in 2004 at The University of Manchester, England. They used sticky tape to remove single layers from the surface of graphite and deposit them onto a silicon wafer. The isolation of Graphene was a breakthrough which ultimately won the 2010 Nobel Prize for Physics.
In its purest form Graphene has a molecular structure comprising of a single layer of Carbon atoms bonded in a hexagonal structure. Graphene possesses an unsurpassed combination of mechanical, electrical, and thermal properties. The Graphene used in Blocksil’s corrosion resistant coating is manufactured using a synthetic, bottom up process that is repeatable, proven and almost completely free of Graphitic impurities, Graphene Oxide or transition metals.
Our Graphene manufacturer and supplier, Applied Graphene Materials (AGM), UK, was founded by Professor Karl Coleman in 2010, with its operations and processes based on technology that he initially developed at Durham University, England. The creation of their Graphene is through a proprietary, patented process.
Andy Gent, Commercial Director at AGM, has worked with Blocksil from the beginning of this project and comments “Blocksil’s idea to use our Graphene within their corrosion resistant roof coating has taken everyone forward in terms of coating technology”.
CW: How does Graphene work in the coating?
Blocksil: The number of atomic layers varies but our Graphene typically has a 1 to 10 nanometre thickness with 1 to 15 microns lateral diameter, resulting in aspect ratios up to 1:1000.
To put this into perspective, the surface area of ten grams will cover a soccer pitch.
This large surface area provides an exceptionally long and tortuous path for any corrosive liquid to work its way through a coating.
Introducing the Graphene into the roof coating was and is a complex process as it cannot just be poured into the mix. The detail of the process is confidential but we can say that there had to be some work on pigmentation. Graphene is Carbon which is black of course. And as soon as one changes one constituent another needs tweaking. But it is here now and all can benefit from the enhanced performance.
CW: What benefits does the Graphene addition give the client?
Blocksil: Tested to ISO 9227 – Neutral Salt Spray, with testing in continuous 5% Sodium Chloride solution at 35oC, our Graphene enhanced coating has taken us past 11,800 hours! To put this into recognizable terms – for a roof we’re giving a 30 year product warranty. And in the automotive industry, coatings tend to be acceptable with up to 1,000 hours.
For more information on how well our Graphene enhanced coating works, Alltimes Coatings have created a highly professional online CPD (Continuous Professional Development) presentation which explains in greater detail just how the Graphene Enhanced Top Coat benefits steel surfaces. Entitled “Rust Never Sleeps”, this CPD is available via Alltimes Coatings (www.alltimescoatings.com).
CW: Do the coating applicators and contractors benefit from having a Graphene coating?
Blocksil: They certainly do. The coating is solvent, isocyanate and VOC free, and is applied as a single coat once the surface has been prepared. Because of its impressive spread rate, contractors can cover much larger surface areas than before and its stop / start technology also means the coating can be applied in stages without any time restrictions. This gives contractors a new level of freedom and flexibility and no adhesion problems with day edges and cut ins.
For elevated jobs scaffolding is needed for less time and safety is greatly improved with operatives spending less time working at height. In addition the coating does not need ‘hazardous storage’, which makes onsite logistics of handling and storage easy.
CW: Is the Blocksil Graphene enhanced coating available worldwide?
Blocksil: At present we’re just supplying the UK though we’re getting interest in the USA through our partner Marc Zirkle, who heads up Blocksil USA. We successfully carried out some coating trials last year in north east Georgia at an engineering works near the Tallulah River.
To date the Graphene Enhanced Top Coat has been approved for use by Avanti Communications, a multinational telecommunications company who operate satellites and the ground station dishes. These dishes are located around the world in often remote and corrosive sites.
The coating is also being rolled out on to communication masts for private and state owned use. These masts tend to be situated on the top of high ground such as mountains and suffer from flexing and high wind flow, both of which seem to increase corrosion levels.
Our next step is to start working with other infrastructure providers such as the railway networks. This is in addition to all the hundreds of steel roofs that have benefited.
CW: So where else can Graphene be used within the coating industry?
Blocksil: Blocksil is certainly working on incorporating it into other coatings, paints and treatments to take advantage of the enhanced corrosion resistance offered.
For example, we’re incorporating Graphene into a primer for use below the Top Coat. Simple you would think? Not quite as we’re also trying to take out all the solvent so we can offer clients a completely solvent free corrosion resistant coating system. This will give obvious benefits to the applicators and the environment.
And we’re working on developing the Top Coat still further to take advantage of some new polymer chemistry we’ve developed with one of our toll manufacturers.
CW: Are you looking at any other coating developments?
Blocksil: Yes, we’d like to make use of our knowledge of infrared reflectance coatings.
The idea is for a coating that reduces the amount of infra-red radiation absorbed by the coating, thereby reducing the amount of heat passed through it. There are clear benefits to be had, with reduced energy usage for air conditioning being one. This modification to the coating will add nothing to the weight or colour of the coating as we will be modifying the pigments and additives already in use.
CW: How will this work?
Blocksil: It is well known that a white or light coloured surface remains cooler than a black, or darker surface thanks to the interaction of the coating with the infra-red radiation emitted by the Sun. As infra-red radiation accounts for approximately 50% of the total energy of solar radiation, reducing the amount absorbed by the coating is clearly beneficial. By modifying the pigments and additives within the coating, Blocksil will be able to improve the Total Solar Reflectance (TSR) of the coating, even with darker colours.
Depending on the coating colour and the levels of brightness, laboratory tests suggest a temperature reduction of between 8.7oC and 14.7oC, with an improvement in the TSR of between 50% and 32%. An additional benefit of having an improved TSR is an enhanced lifespan of the coating. The reduced surface temperature will reduce any thermal degradation and temperature differences between day and night, direct sunlight and shadowed areas. This in turn would lead to reduced thermal warping and stress.
CW: How would you summarise Blocksil’s position?
Blocksil: Blocksil will continue our efforts to bring the very latest ideas and technology to the coating industry. Chris Knowles, Chief Technical Officer at Blocksil comments that “we believe there are opportunities for developing and cross benefitting different industries’ coatings away from older, less efficient coatings and we’re certainly well placed to help that happen”.
References:
1 National Association of Corrosion Engineers
2 Allied Market Research