06.22.21
A technology solution from Georgia-Pacific Chemicals (GPC), Customer Inventory Tracking (CIT), now tracks resin inventory and displays it via a web-based dashboard. The data is then used by GPC customers to optimize order profiles. Based previous two-week or 24-hour usage, the system can suggest canceling, moving, or placing additional orders as needed for optimal efficiency.
CIT works by utilizing the mill’s current digital level monitoring of its resin tanks. Data from the system is sent to Georgia-Pacific Chemicals where the data is transformed, based on that mill’s unique operations, into a dashboard that can be accessed on either desktop or mobile devices and only by designated personnel.
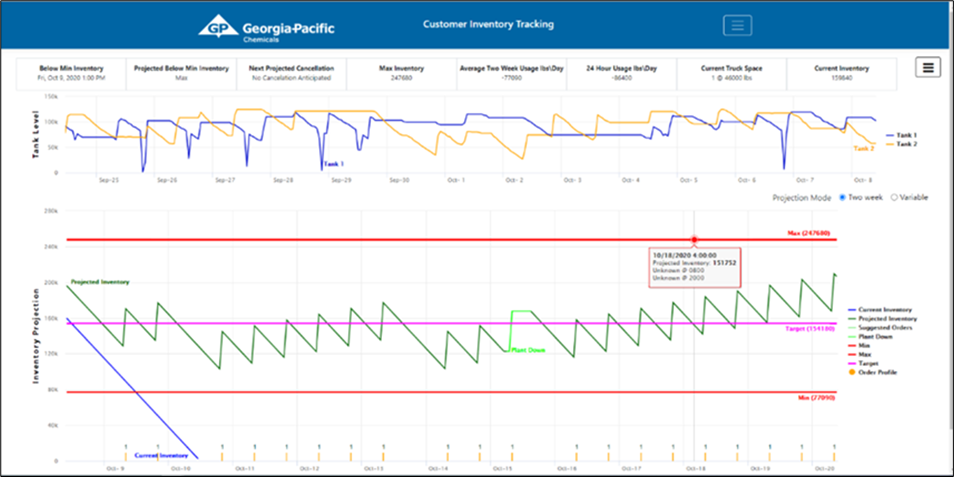
Sample Dashboard for Customer Inventory Tracking System
The system even allows scheduling upcoming downtime so orders can be adjusted accordingly far in advance of the downtime. The Customer Inventory Tracking service, using data as recently as the last hour, can predict further out than the standard 12 days shown on the dashboard.
Optional features of the Customer Inventory Tracking System from GPC include email alerts for order cancelation, tank cycling, projected inventory going below minimum or to zero, or a bad tank sensor.
The service can help a plant to reduce working capital, downtime, quality issues related to tank rotation, and costs related to rushed and/or canceled orders.
“The Customer Inventory Tracking service can be managed collaboratively or solely by Georgia-Pacific Chemicals,” said Jason Halmo, Project Manager. “Some customers might want us to handle the process entirely so they can concentrate on making product and growing their business.”
CIT works by utilizing the mill’s current digital level monitoring of its resin tanks. Data from the system is sent to Georgia-Pacific Chemicals where the data is transformed, based on that mill’s unique operations, into a dashboard that can be accessed on either desktop or mobile devices and only by designated personnel.
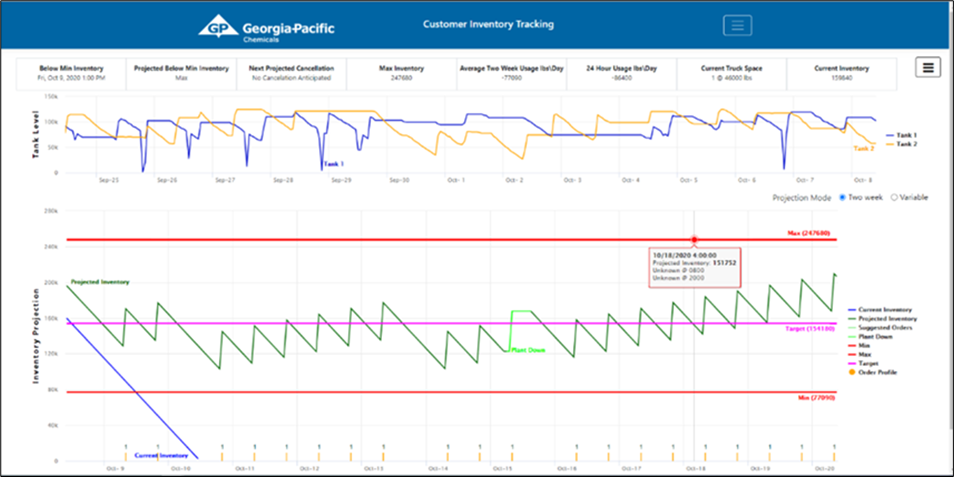
Sample Dashboard for Customer Inventory Tracking System
Optional features of the Customer Inventory Tracking System from GPC include email alerts for order cancelation, tank cycling, projected inventory going below minimum or to zero, or a bad tank sensor.
The service can help a plant to reduce working capital, downtime, quality issues related to tank rotation, and costs related to rushed and/or canceled orders.
“The Customer Inventory Tracking service can be managed collaboratively or solely by Georgia-Pacific Chemicals,” said Jason Halmo, Project Manager. “Some customers might want us to handle the process entirely so they can concentrate on making product and growing their business.”