Dhanush Honnappa, Senior Research Associate, Grand View Research11.16.18
Powder coatings have emerged as the new staple in myriad applications and have contributed significantly to the global coatings market. Substitution of conventional coatings with powder coatings is expected to contribute to the healthy projection of the market. Powder coatings, which are available in powdered or free-flowing form, does not involve the use of solvents compared to liquid coatings and hence offers environmental sustainability.
\
The raw materials employed in powder coating formulation include polyurethane (PU), polyester (PE), fusion-bonded epoxy, polyester epoxy, hybrid epoxy, and straight epoxy. The formulation process involves multiple stages, principally encompassing batching, concoction/premixing, extrusion, and particle size reduction.
The key coating methods employed in the industry include electrostatic spray and fluidized bed. Electrostatic spray method is gaining traction in the manufacturing industry owing to its functional advantages such as high transfer efficiency, less impact on the environment, ease of color change, and enhanced finish quality. In addition, the increased adoption of powder coat guns in electrostatic sprays has emerged as a key trend in the market.
Radical developments associated with the application of powder coatings are concurrent with the advancements in coating technology. For instance, in-mold powder coating involves the spraying of the coating material onto a mold cavity (heated). The upshot of this process is to achieve impact resistant and chip resistant coatings. Other advancements in the market include the development of color-keyed powder primer technology. This technology has gained a wide acceptance among automotive component manufacturers across the world.
The superior properties associated with powder coatings make them ideal for use in an array of applications. Their use minimizes the emission of volatile organic compounds and offers a thicker coating in comparison with conventional liquid coatings.
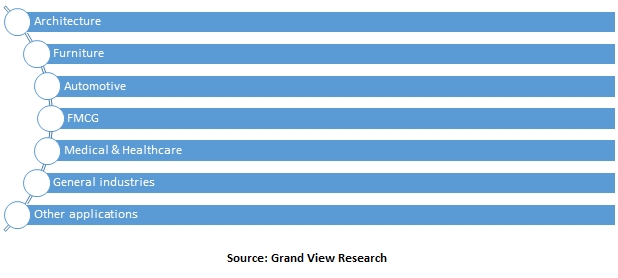
The growing demand for chip resistant and tough automotive components has established powder coatings as a popular finishing technique in the automotive sector. According to Grand View Research, the automotive segment dominated the global powder coatings market in 2017 and is expected to sustain its prominent position over the forecast period. Powder coatings have been garnering unprecedented demand from automotive OEMs owing to rising appeal of automotive colors.
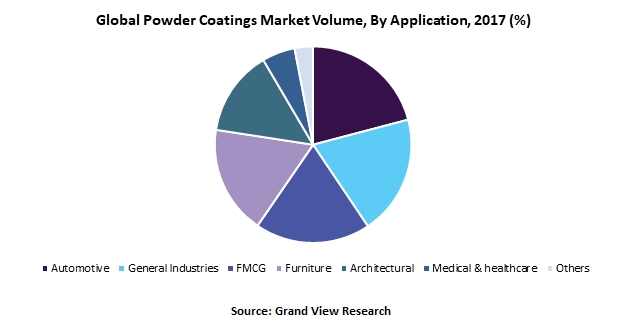
Grand View Research identifies the furtherance of technology to be a key driving factor for the powder coatings market. Notwithstanding the high growth opportunities for powder coating manufacturers in the automotive sector, the market has offered a host of technological advancements relating to raw materials, instrumentation, and pigmentation. In this regard, key market players have seized growth opportunities to strengthen their market position. For instance, in 2017, Evonik Industries AG debuted powder coatings under the brand VESTAKEEP designed for various industrial applications to withstand extreme environmental conditions.
In the past few years, new raw material suppliers in the powder coatings market have focused on innovations to improve the production process. One such innovation is the development of self-healing coating technology by Autonomic Materials, Inc. (AMI). This technology employed microcapsules derived from core-shell morphology. Such futuristic developments in the industry have encouraged manufacturers to target new and prospective business segments.
The robust manufacturing base of automotive industry in countries such as China, India, and Japan, has strengthened the powder coatings market in this region. The extent of powder coatings usage in automotive components is principally driven by the rising sale of vehicles, most notably passenger vehicles, in the region. Proximity to raw material suppliers, less stringent laws on the emission of VOCs, and low labor costs have encouraged the powder coating manufacturers to set up businesses in this region.
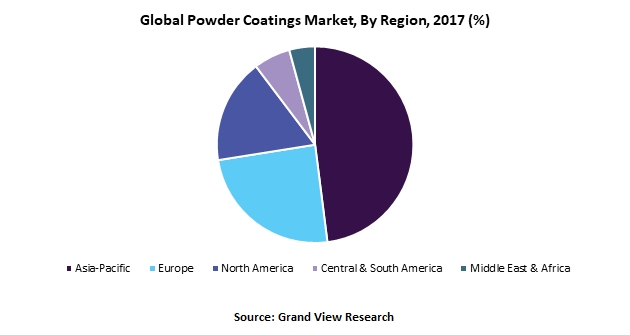
The need for a significant breakthrough in the powder coatings market has extended the application scope of powder coatings. Jewelry artists (abstract) have started using powder coatings owing to benefits such as enhancement of aesthetics, durability, and toughness. Powder coatings are used for various metal arts, such as the coating of sculptures, on account of the long-lasting protection provided to metals in all weathering situations. Building facades emerged to be one of the novel applications of powder coatings in the U.S., backed by the spurring demand for custom designs while offering protection to the surfaces.
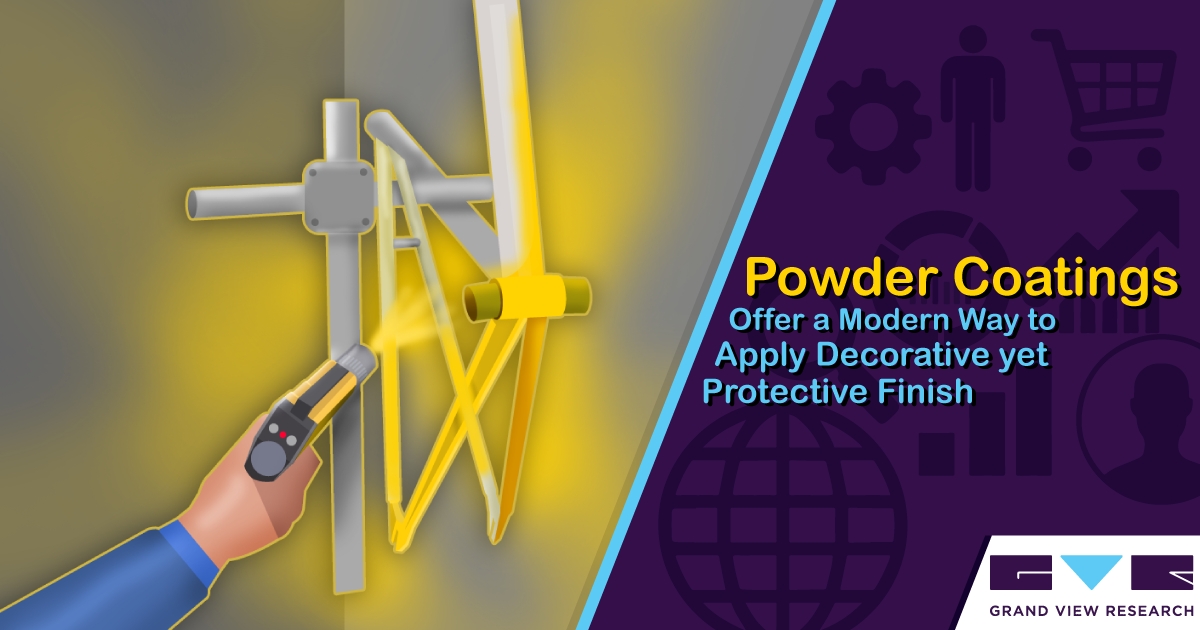
The global powder coatings market is fragmented and marked by the presence of domestic and international players. Key market players include Akzo Nobel N.V., Jotun, PPG Industries, Inc., Kansai Paint Co., Ltd., Axalta Coating Systems, NIPPON PAINT Co., Ltd., BASF SE, The Sherwin-Williams Company, The Valspar Corporation, Royal DSM, Bayer AG, Evonik Industries AG, Arkema S.A., Ferro Arte de Mexico, EISENMANN SE, TCI Powder, and Allnex Holding S.à r.l.
The market is subject to witness intense competition among manufacturers. The prominent players have employed strategies to withstand competition in the market. Product development and mergers & acquisitions have been the key strategies implemented by the market players. For instance, Axalta Coating Systems presented two novel corrosion resistant and high-temperature internal pipe coatings under the brand Nap-Gard. The merger between The Sherwin-Williams Company and The Valspar Corporation was one of the biggest agreements in the industry and redefined the prominence of contracting parties in the market. Furthermore, in June 2016, PPG Industries announced its plan to acquire Metokote Corporation to extend its coating services to consumers.
Global powder coatings market is driven by the increasing application of powder coatings across end-use sectors such as industrial and consumer goods. The business landscape concerning the market is fueled by product development in Asia Pacific. The powder coatings industry creates lucrative opportunities for manufacturers to penetrate untapped markets in this region, thereby creating new avenues for attracting customers. The market is consolidating, which is expected to be a favored strategy by the stakeholders. The market participants have focused on purchasing leverage and pricing power while assuring production efficiency.
The high costs of investment associated with setting up a business have discouraged the key automotive component manufacturers from entering the powder coatings market. Therefore, these players outsource their powder coating requirement from third-party or tier one manufacturers. The OEMs have benefited from customized powder coating solutions offered by third parties, in spite of the costs involved in outsourcing. This has aided the OEMs in sustaining their brand reputation while creating new market avenues. However, the possibility of backward integration in the market is expected to offer substantial impetus to the market over the forecast period owing to a considerable increase in the scale of operation.

The raw materials employed in powder coating formulation include polyurethane (PU), polyester (PE), fusion-bonded epoxy, polyester epoxy, hybrid epoxy, and straight epoxy. The formulation process involves multiple stages, principally encompassing batching, concoction/premixing, extrusion, and particle size reduction.
The key coating methods employed in the industry include electrostatic spray and fluidized bed. Electrostatic spray method is gaining traction in the manufacturing industry owing to its functional advantages such as high transfer efficiency, less impact on the environment, ease of color change, and enhanced finish quality. In addition, the increased adoption of powder coat guns in electrostatic sprays has emerged as a key trend in the market.
Radical developments associated with the application of powder coatings are concurrent with the advancements in coating technology. For instance, in-mold powder coating involves the spraying of the coating material onto a mold cavity (heated). The upshot of this process is to achieve impact resistant and chip resistant coatings. Other advancements in the market include the development of color-keyed powder primer technology. This technology has gained a wide acceptance among automotive component manufacturers across the world.
The superior properties associated with powder coatings make them ideal for use in an array of applications. Their use minimizes the emission of volatile organic compounds and offers a thicker coating in comparison with conventional liquid coatings.
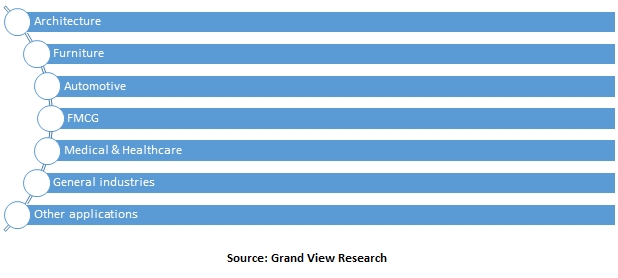
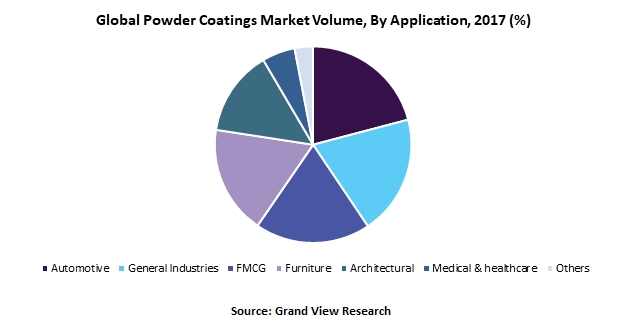
In the past few years, new raw material suppliers in the powder coatings market have focused on innovations to improve the production process. One such innovation is the development of self-healing coating technology by Autonomic Materials, Inc. (AMI). This technology employed microcapsules derived from core-shell morphology. Such futuristic developments in the industry have encouraged manufacturers to target new and prospective business segments.
The robust manufacturing base of automotive industry in countries such as China, India, and Japan, has strengthened the powder coatings market in this region. The extent of powder coatings usage in automotive components is principally driven by the rising sale of vehicles, most notably passenger vehicles, in the region. Proximity to raw material suppliers, less stringent laws on the emission of VOCs, and low labor costs have encouraged the powder coating manufacturers to set up businesses in this region.
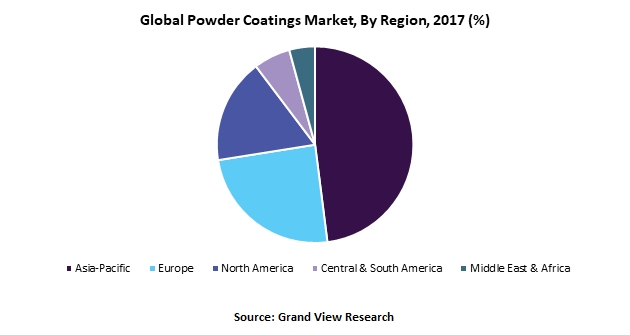
The need for a significant breakthrough in the powder coatings market has extended the application scope of powder coatings. Jewelry artists (abstract) have started using powder coatings owing to benefits such as enhancement of aesthetics, durability, and toughness. Powder coatings are used for various metal arts, such as the coating of sculptures, on account of the long-lasting protection provided to metals in all weathering situations. Building facades emerged to be one of the novel applications of powder coatings in the U.S., backed by the spurring demand for custom designs while offering protection to the surfaces.
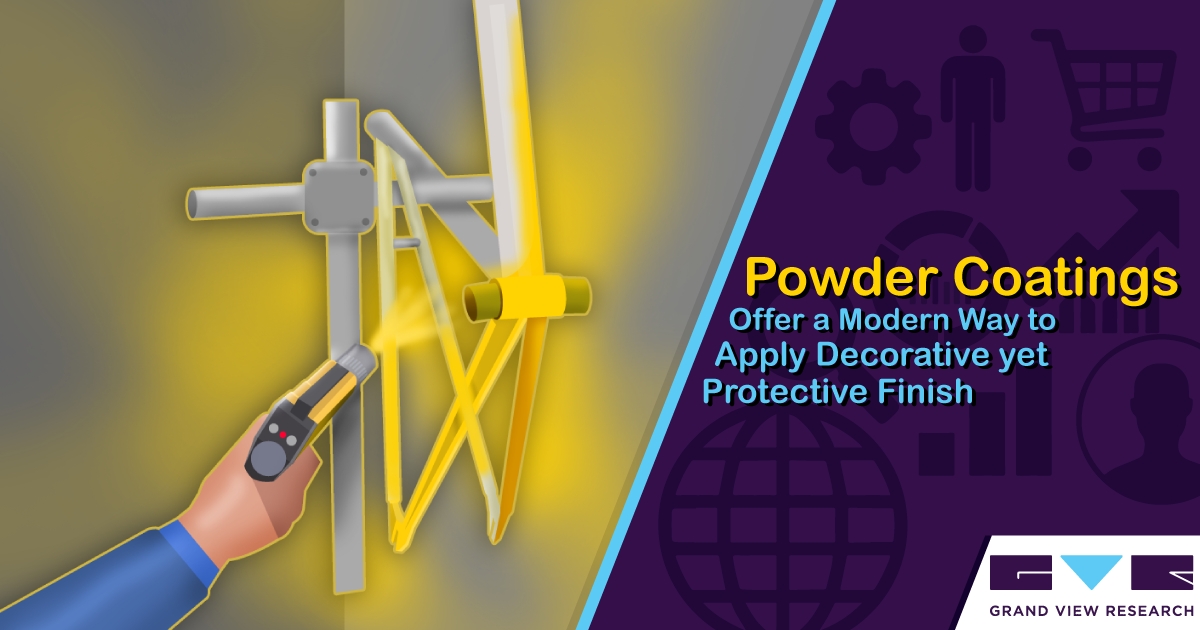
The market is subject to witness intense competition among manufacturers. The prominent players have employed strategies to withstand competition in the market. Product development and mergers & acquisitions have been the key strategies implemented by the market players. For instance, Axalta Coating Systems presented two novel corrosion resistant and high-temperature internal pipe coatings under the brand Nap-Gard. The merger between The Sherwin-Williams Company and The Valspar Corporation was one of the biggest agreements in the industry and redefined the prominence of contracting parties in the market. Furthermore, in June 2016, PPG Industries announced its plan to acquire Metokote Corporation to extend its coating services to consumers.
Global powder coatings market is driven by the increasing application of powder coatings across end-use sectors such as industrial and consumer goods. The business landscape concerning the market is fueled by product development in Asia Pacific. The powder coatings industry creates lucrative opportunities for manufacturers to penetrate untapped markets in this region, thereby creating new avenues for attracting customers. The market is consolidating, which is expected to be a favored strategy by the stakeholders. The market participants have focused on purchasing leverage and pricing power while assuring production efficiency.
The high costs of investment associated with setting up a business have discouraged the key automotive component manufacturers from entering the powder coatings market. Therefore, these players outsource their powder coating requirement from third-party or tier one manufacturers. The OEMs have benefited from customized powder coating solutions offered by third parties, in spite of the costs involved in outsourcing. This has aided the OEMs in sustaining their brand reputation while creating new market avenues. However, the possibility of backward integration in the market is expected to offer substantial impetus to the market over the forecast period owing to a considerable increase in the scale of operation.