Kerry Pianoforte, Editor 02.28.17
Integricote® Inc. is an advanced-materials company headquartered in Houston, Texas. From the inception of Integricote it has been commercializing its unique range of technology since 2013, the goal being to work primarily in the construction markets specializing on sealing masonry and providing stain/water repellency solutions to the timber market. These efforts have materialized into the CaraPro® range of products and used for water repellency, staining wood, stucco and grout, porous tiles and brickwork, masonry & concrete. The patented technology Integricote uses comes from the University of Houston’s (UH) nanotechnology labs at the Institute for NanoEnergy. This technology was led by pioneering nanotechnologist, Prof. Seamus Curran and his team of faculty, post-doctoral researchers, and PhD students. Although it generally takes many years to build a nanotech based company and in most instances tens of millions of dollars in venture funding; Integricote has done this on a shoestring budget using a lean model instead. The products are now in the market primarily serving Texas and have been for the last 15 months.
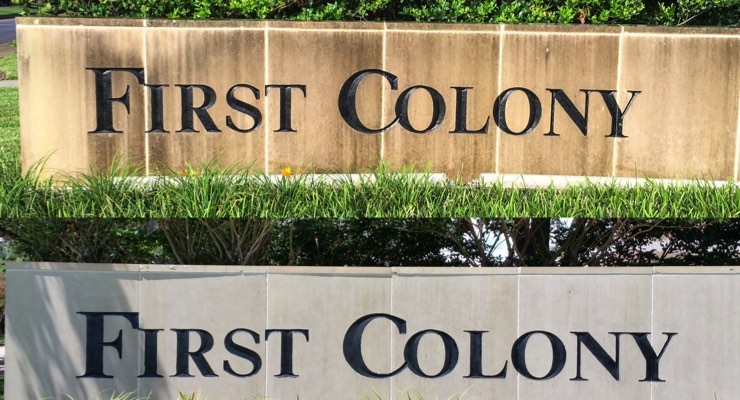
Coatings World recently had the opportunity to interview Prof. Curran who serves as CEO of Integricote.
What types of coatings products does your company produce, what are their applications?
Prof. Curran: When people think of coatings they think in the end of paints which is simply another way to cover off the surface underneath. This may be fine for interior walls and there are times when this may be necessary as the look of the surface underneath is not so important. However, when we look at fine brickwork, decks or fences; painting jobs gives surfaces such a plastic look. This takes away from the beauty of the thing you want to protect.
Integricote’s primary technology was developed so that we can maintain the aesthetics of material such as stone tiles, brickwork or wood finishes without that fake painted look. The products Integricote has developed are a series of penetrating sealers. They are applied by firstly spraying (or brushing) onto a surface. This allows the product to seep into its pores and actually becomes part of the material it wants to protect.
We have coated with these penetrating sealers structures such as walkways and bridges; wooden pergolas and pavilions; stained decks and fences; sealed concrete driveways and the front facades of buildings as well as swimming pool areas and brick walls.
What sets your company’s products apart from similar products on the market?
Curran: Two fundamental facets comprise the cornerstone of our technology. First, the penetrating aspect used by our technology when applied to porous surfaces to provide protection. Second, the ability of our material to also function as a penetrating delivery system for an assortment of functional additives such as fungicides/mildewcide and termiticide/insecticides. In contrast to the vast majority of our competitors who use carbon or oil based products, our molecular system penetrates through porous materials. It then interacts with the molecular structure of a host such as wood or masonry materials and becomes part of it by bonding to it. As a consequence it forms a three-dimensional protective barrier against the elements and also a network in which to embed other additives. In contrast, conventional sealers, lacquers, varnishes, enamels, or glosses that merely form an easily erodible surface coating.
Integricote’s CaraPro range of products are sophisticated materials built at the nanoscale (very small molecules). In effect, they form a tailorable protective interpenetrating network that seeps into a material to forming a nano-/micro-structured barrier from the inside out. This barrier is designed to lock in desired properties but reducing and in some instances preventing harsh environmental damage for a long period of time. This accommodates the option of imparting a variety of selective functionalities to the bulk of wood and masonry such as color or some form of antimicrobial additives.
How does this work? When we add in other functionalities such as pigments used for colors/staining or biocides, they are likewise carried along with our molecules in solution as they are coated on the surface. They flow with the solvent underneath the surface and keep flowing until the solvent evaporates. Once the solvent is gone our molecules are immediately to form this network by bonding to each other and also to the host material they are to protect such as the fibers in wood or pores in masonry. In doing so they also lock in the additives that flowed in with them, keeping those additives in place. This prevents leaching effects outside physical damage to the substrate and will resist water penetration, providing additional but long lasting functionalities.
In what areas is your company focusing its R&D?
Curran: The roadmap for creating our next generation of effective, commercializable products with applications spanning a diverse number of industries is exciting. Having a very highly successful teams of researchers and entrepreneurs which make up the core of our business team; there are a whole host of technologies ready to be developed and sold. Imagine a product that could reduce if not remove the need for pressure treatment of wood and how this could shake up the timber market. Or in another case, a spray on stain and protective coating for wood that can encapsulate and provide almost complete termite resistance using a very benign pesticide. If there is another oil spill in rivers or the sea, we have a technology already available that can soak up hydrocarbons but is still water repellant which can be used over and over, with the added benefit of being also able to separate and save the hydrocarbons.
As a technology company this is critical to the value of the business. Making sure we are not just one step ahead of our competitors but on a completely different platform gives us the edge a small company in a crowded materials space dominated by billion dollar companies. The next few years of technologies just for the construction industry has already been developed, while other markets have yet to be addressed there are also solutions that could be applied for energy, fabrics and environmental protection.
Does your company have any plans for expansion?
Curran: It is an exciting time for Integricote and its employees. A state of the art product testing and development laboratory adjacent to a new formulation processing facility have just come online in the first quarter of 2017. Situated in the heart of the University of Houston’s innovation hub, this new facility will allow the needed expansion of operations to meet product demand for the medium term. Our expansion plans are of course to go from local to regional and eventually national distribution with our products. We are in negotiations with a number of groups for the larger distribution options who we hope to partner up with and will announce later in the year.
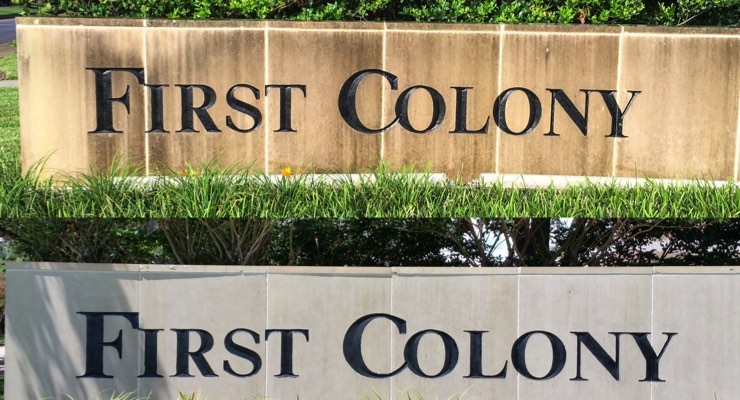
Coatings World recently had the opportunity to interview Prof. Curran who serves as CEO of Integricote.
What types of coatings products does your company produce, what are their applications?
Prof. Curran: When people think of coatings they think in the end of paints which is simply another way to cover off the surface underneath. This may be fine for interior walls and there are times when this may be necessary as the look of the surface underneath is not so important. However, when we look at fine brickwork, decks or fences; painting jobs gives surfaces such a plastic look. This takes away from the beauty of the thing you want to protect.
Integricote’s primary technology was developed so that we can maintain the aesthetics of material such as stone tiles, brickwork or wood finishes without that fake painted look. The products Integricote has developed are a series of penetrating sealers. They are applied by firstly spraying (or brushing) onto a surface. This allows the product to seep into its pores and actually becomes part of the material it wants to protect.
We have coated with these penetrating sealers structures such as walkways and bridges; wooden pergolas and pavilions; stained decks and fences; sealed concrete driveways and the front facades of buildings as well as swimming pool areas and brick walls.
What sets your company’s products apart from similar products on the market?
Curran: Two fundamental facets comprise the cornerstone of our technology. First, the penetrating aspect used by our technology when applied to porous surfaces to provide protection. Second, the ability of our material to also function as a penetrating delivery system for an assortment of functional additives such as fungicides/mildewcide and termiticide/insecticides. In contrast to the vast majority of our competitors who use carbon or oil based products, our molecular system penetrates through porous materials. It then interacts with the molecular structure of a host such as wood or masonry materials and becomes part of it by bonding to it. As a consequence it forms a three-dimensional protective barrier against the elements and also a network in which to embed other additives. In contrast, conventional sealers, lacquers, varnishes, enamels, or glosses that merely form an easily erodible surface coating.
Integricote’s CaraPro range of products are sophisticated materials built at the nanoscale (very small molecules). In effect, they form a tailorable protective interpenetrating network that seeps into a material to forming a nano-/micro-structured barrier from the inside out. This barrier is designed to lock in desired properties but reducing and in some instances preventing harsh environmental damage for a long period of time. This accommodates the option of imparting a variety of selective functionalities to the bulk of wood and masonry such as color or some form of antimicrobial additives.
How does this work? When we add in other functionalities such as pigments used for colors/staining or biocides, they are likewise carried along with our molecules in solution as they are coated on the surface. They flow with the solvent underneath the surface and keep flowing until the solvent evaporates. Once the solvent is gone our molecules are immediately to form this network by bonding to each other and also to the host material they are to protect such as the fibers in wood or pores in masonry. In doing so they also lock in the additives that flowed in with them, keeping those additives in place. This prevents leaching effects outside physical damage to the substrate and will resist water penetration, providing additional but long lasting functionalities.
In what areas is your company focusing its R&D?
Curran: The roadmap for creating our next generation of effective, commercializable products with applications spanning a diverse number of industries is exciting. Having a very highly successful teams of researchers and entrepreneurs which make up the core of our business team; there are a whole host of technologies ready to be developed and sold. Imagine a product that could reduce if not remove the need for pressure treatment of wood and how this could shake up the timber market. Or in another case, a spray on stain and protective coating for wood that can encapsulate and provide almost complete termite resistance using a very benign pesticide. If there is another oil spill in rivers or the sea, we have a technology already available that can soak up hydrocarbons but is still water repellant which can be used over and over, with the added benefit of being also able to separate and save the hydrocarbons.
As a technology company this is critical to the value of the business. Making sure we are not just one step ahead of our competitors but on a completely different platform gives us the edge a small company in a crowded materials space dominated by billion dollar companies. The next few years of technologies just for the construction industry has already been developed, while other markets have yet to be addressed there are also solutions that could be applied for energy, fabrics and environmental protection.
Does your company have any plans for expansion?
Curran: It is an exciting time for Integricote and its employees. A state of the art product testing and development laboratory adjacent to a new formulation processing facility have just come online in the first quarter of 2017. Situated in the heart of the University of Houston’s innovation hub, this new facility will allow the needed expansion of operations to meet product demand for the medium term. Our expansion plans are of course to go from local to regional and eventually national distribution with our products. We are in negotiations with a number of groups for the larger distribution options who we hope to partner up with and will announce later in the year.