Kerry Pianoforte, Editor06.17.15
The market for industrial coatings is a highly segmented market that includes such diverse segments as offshore oil and gas, commercial architecture, general industrial and industrial maintenance. Industrial coatings manufacturers interviewed by Coatings World reported that while growth rates have slowed in some segments, others segments, such as oil and gas, are driving growth.
“We track the external market trends in a number of our global end use markets such as industrial production, commercial construction new builds, transportation builds, electrical motor production and pipeline miles constructed,” said Michael Cash, senior vice president and president, industrial coatings, Axalta Coating Systems. “Our best estimate based on aggregated third party data is that the global industrial coatings end markets grew by three to four percent in 2014. By working closely with our customers, and by welcoming many new customers to the Axalta family in 2014, we were able to grow faster than the overall size of a number of our end use markets last year.”
“The industrial coatings market covers a large and diverse range of segments and applications,” said Shelley J. Bausch, vice president, Global Industrial Coatings, PPG. While growth rates have slowed in some of these segments due to end market reductions (such as heavy duty equipment), others continue to deliver strong growth performance. With PPG’s global capabilities, we have been able to leverage these areas of growth to continue to outpace the market.
“Additionally, as customers continue to look for ways to improve performance and provide new functionality to their end products, new areas of growth are evolving for coatings,” Bausch added. “High performing coatings can be used to meet multiple needs, reducing the need for specific substrates or replacing mechanical solutions.”
Sherwin-Williams has seen growth in several areas, including wood finishing, general finishing, heavy equipment and building products. “One market that we’re particularly excited about is OEM prefinished residential and commercial wood flooring coatings market in which we just announced our participation,” said Nick Bartoszek, global marketing director – liquid and powder products, Sherwin-Williams. “In all of the markets we serve, customers are asking for products that offer low or zero-VOC solutions, as well as ways to improve their finishing processes. We look for ways to become a true partner with our customers, providing expertise that offers guidance well beyond the product.”
According to Klaus Moller, Hempel group vice president of marketing and business development, the general market for industrial coatings grew by approximately three percent between 2013 and 2014. “In general, the industry was boosted by government investment in infrastructure projects, especially in the Middle East and Asia, he said. “We expect the overall industrial coatings market to grow inline with global GDP. We foresee that commercial architecture will show a growth rate above that of the overall market while oil and gas growth rates look more uncertain due to the current low oil and gas prices.”
The industrial coatings market comprises many diverse segments – each offering its own set of opportunities and challenges. “Each application segment presents unique growth opportunities,” said Bausch. “Globally, expansions in oil and gas and transportation of these commodities provide multiple coatings opportunities. Trends in electronic materials and their use beyond computers and mobile phones to automobiles, commercial buildings, and homes provides a diverse growth opportunity for coatings. And as a macro trend, the continued expansion of the transportation market – personal and commercial vehicles – gives a robust opportunity for growth. This is particularly apparent in developing regions.”
“Trends in construction segments are mixed, both geographically and by application segment,” Bausch added. “However, the need for coatings in these segments continues to be robust. And finally, new and increased performance requirements also are driving growth opportunities. As an example, we see tremendous opportunity for growth on frames and chassis in the automotive and transportation segments through their growing demand for improved corrosion resistance. With the continued strength of the automotive sector, this will be positive for industrial coatings.”
Sherwin-Williams is witnessing and responding to growth opportunities across all segments. “For wood finishing, Sherwin-Williams introduced our Ultra-Cure Waterborne UV Topcoats for our wood finishing customers who are looking for flatline finishing technology to help meet regulatory requirements while also increasing productivity,” said Bartoszek. Recently, formaldehyde in wood finishing has also been in the news; we offer a full line of formaldehyde-free lacquers, conversion varnishes, primers and surfacers for manufacturers that wish to address this issue. In some cases, use of these products has helped end users meet LEED certification.”
“In general finishing applications, new resin developments can yield lower VOCs and reduced HAPs in polyurethane coatings, which help finishers meet sustainability goals, save money on energy and equipment, without sacrificing appearance,” added Bartoszek. “Heavy equipment manufacturers typically have firm coating specifications in place, so helping them and their tier suppliers take cost out of the coating process by working with them to gain efficiency continues to be paramount. In building products, architects and specifiers need to meet stringent AAMA 2605-13 specifications for coatings to meet long-lasting performance standards in a variety of weather conditions. As the only U.S. licensee for Arkema Kynar 500 FSF PVD Resin, we think we are in a good position to help them meet those standards, using 100 percent Kynar in our SHER-NA 5000 Fluorosurfactant-free architectural coating. And for the prefinished wood flooring market, we’re offering a new family of prefinish coatings that includes UV-curable wood flooring coating systems.”
Cash said that one of the strengths of Axalta’s industrial business is the global product portfolio it offers which, combined with strong sales teams around the world, can match potential growth distribution in different regions. “This is key because end use segments can grow at different rates in different economic regions,” said Cash. “For example, there’s anticipated growth in drilling, albeit at different rates of growth in different geographies, which provides markets for our Nap-Gard FBE products. Similarly, faster rates of industrialization in China and elsewhere in Asia suggest room for growth in commercial construction and the industrial maintenance market.”
Industrial coatings manufacturers continue to be challenged to meet cost and performance requirements. First and foremost, customers expect their coatings to meet the most stringent performance requirements.
“The coating has to work; that’s a given,” said Bartoszek. “You’re really not in the game if the coating doesn’t meet the customer’s needs. We see our differentiator as the ability to provide expertise and improvement beyond the sale of the product. In some cases, that may actually mean selling less of a coating through process improvements. But helping a customer take costs out of the process through collaboration, or helping them meet sustainability goals, is a worthwhile endeavor. We seek to partner with our customers because we know that if they succeed in all aspects of their finishing process, we’ll be working together for a long time to come.”
“To meet their business demands, they need us to provide coatings that improve corrosion performance, provide additional functionality and support light-weighting or other substrate changes,” said Bausch. “From a cost and efficiency perspective, they need us to provide solutions that accelerate production throughput, enable faster cure times, utilize lower cure temperatures, and reduce process steps. Continual improvement of environmentally friendly coatings represents another key area for increasing performance and delivering our customers a competitive advantage. PPG is pursuing advances in each of these areas, regardless of industry, geography or legislation.”
“Our industrial coating customers are looking for a paint company that will become natural extensions of their business and offer a true understanding for what will help them become successful,” said Cash. “This can happen through superior product performance as well as the technical service and support we provide onsite to help our customers achieve their performance goals. It is one thing to provide superior, innovative products, but it is truly an achievement to help our customers benefit from the full capability of our products in the unique coating application environments of their businesses.”
Customers needs are dependent on the specific application. “Owners and engineering companies typically look for long-term corrosion performance verified according to recognized performance standards, such as ISO or NORSOK,” Moller said. “In addition, specific performance criteria, such as chemical and heat resistance, can play an important role for customers when selecting coatings for more demanding and specialised applications. Fabricators and applicators usually focus on the application properties of the coating, such as drying time, over-coating intervals and surface preparation requirements.”
Moller added that all customers would like to reduce their overall costs. “End users, therefore, look for a longer lifecycle for their investments and a lower total coating cost, including costs associated with application and surface preparation. Many applicators, particularly in shipyards and fabrication factories, can reduce costs by increasing productivity through the use of more surface-tolerant coating systems or faster drying systems. These systems also enable applicators and owners to reduce their carbon footprint. Fast-curing products enable steel fabricators to reduce the energy used to heat drying halls, for example.”
Industrial coatings manufacturers have launched a diverse lineup of products. This year PPG has introduced four new industrial coatings that the company believes represent significant advances in the industrial coatings industry.
“One example is our new VERSABOND pretreatment system,” said Bausch. “This product features a proprietary hypernucleation technology that improves the corrosion resistance of mixed-metal substrates on auto parts and accessories while enabling manufacturers to extend bath life, reduce sludge and lower process temperatures to save energy. By enabling the use of lighter mixed-metal substrates, Versabond pretreatment also supports the broader industry strategy to make vehicles lighter.”
PPG launched ENVIROCRON HTE (high-transfer-efficiency) powder coatings. These products feature a cross-link polymer that enables them to penetrate and apply evenly to metal parts and product assemblies with complex surfaces such as refrigerator racks, patio tables and architectural components.
PPG also launched PERFORMALOC advanced productivity coatings. “These coatings represent an entirely new category of products because they cure fast and hard without baking or forced drying, which makes them ideal for OEMs with limited or no oven-cure capabilities,” added Bausch.
Over the past year Axalta has launched or expanded the global footprint of quite a few products designed for the industrial market and which, in some cases, also serve its large transportation customer base.
“A few examples of the products we have launched in the past year include the global launch of Alesta powder coatings architectural product line and color collection,” said Cash. “The Alesta Global Color Collection is designed to provide assured long-term protection of monumental architectural structures with an innovative color range. We introduced the Alesta ZeroZinc next generation zinc-free anticorrosion powder primers. Our Imron EY High Productivity Basecoat and 8890S Clearcoat system for the commercial vehicle market was added to the Imron family. It is designed to improve throughput and reduce delivery times by allowing for a shorter bake and provide customers with options to meet production demands and save money. Axalta SE6000 Scratch and Mar Resistant Clearcoat was introduced and is designed to provide increased protection within the high use sport vehicle markets where we have a strong position today. The patented dual cure nature of the chemistry allows for faster cure and improved hardness on cool down, to enhance the overall protection while providing premium appearance.”
Sherwin-Williams has several new products that will be introduced throughout the remainder of 2015. Recent new product releases include Powdura OneCure, a two-coat mono-cure system for heavy equipment and general finishing, Ultra-Cure Waterborne UV Topcoats for wood finishing and Prefinish coatings for wood flooring.
Hempel has launched a number of new products recently. AvantGuard technology is a new zinc technology that increases zinc activation to significantly improve the anti-corrosive performance and mechanical strength of the coating without increasing zinc content. Activated zinc products are specially designed for harsh environments. They provide increased corrosion protection and are easy to apply. As a result, they are redefining protection, redefining durability and redefining productivity.
Corrosion under insulation (CUI) is a major challenge and costs process industries significant lost revenue from downtime, repeated maintenance and replacement of corroded parts. “Versiline CUI uses carefully selected barrier pigments to make it highly effective against corrosion under insulation, even under cyclic conditions,” continued Moller. “In addition, its excellent heat-resistant properties make it extremely resistant to micro cracking, even when subjected to extreme temperatures, from cryogenic (-196ºC) up to 650ºC.”
Another new product from Hempel is HEMPACORE intumescent coatings. The product insulates structural steel so it can retain its load-bearing capacity for up to two hours in a fire, giving people valuable time to evacuate.
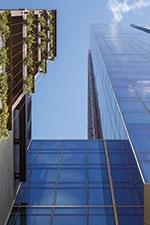
Weathered steel is a popular architectural material thanks to its rich, mottled appearance, but it comes at a high price. The architects at HKS Hospitality Group in Dallas, Texas, were reminded of this as they were in the process of designing the new JW Marriott Convention Center Hotel in Austin. The original concept for the building was to integrate natural materials that are found within the Texas landscape. For the façade of the 34-story primary tower, HKS HG wanted a weathered metal appearance, but when the team saw the estimate to use weathered steel, they knew the price was too high, even for a luxury brand like JW Marriott.
Hunt Construction, the contractor on the project, reached out to ProCLAD Inc., the metal wall design company it had previously worked with on a JW Marriott in Indianapolis. Representatives from Hunt, ProCLAD and HKS consulted closely to determine if there was an alternative solution that could deliver the appearance of weathered steel at a lower price. The architects wanted dimensional panels with varied colors that would read well from far away, since the panels would be installed on the high-rise portion of the building. Craig Caudill, executive vice president for ProCLAD, suggested using formed Galvalume panels painted in dark, medium and light shades to mimic the appearance of rusted steel. Caudill knew that using a variety of colors of Valspar Fluropon coatings could help create the dimensional variety the architects were looking for. Additionally, the coating would maintain its look for years to come, as Fluropon is known for its durability, exceptional color retention, and resistance to chalking and chemical degradation.
“The hard part started then,” said Caudill. The team liked the idea, but wanted to see a sample before committing, and they needed it fast. ProCLAD contacted Valspar, which was able to color match the three shades, work with Western Extrusion to coat them on steel flat stock, and ship them to ProCLAD in less than two weeks. ProCLAD then wheeled a wall mockup of the sample panels onto the HKS lot.
The architects liked the appearance of the panels as well as the lower cost of the solution, but still weren’t ready to commit to the colors.
“HKS provided us with a few paint samples and requested to see five new sets of colors in varying shades of brown, along with a few metallic options,” said John H. Kelly, metal buildings market manager for Valspar. “Clients typically request one or two color variations, but in this instance, we needed to create nearly 20 color options to ensure the best possible result for the client.”
Rising to the challenge, Valspar’s lab team was able to complete the project between Christmas and New Year’s Day, so ProCLAD was able to show HKS 15 new panel mockups shortly after the New Year. Once the color formulations were created, the lab worked cohesively with the Western Extrusion team to quickly spray the oversized panels and have them shipped to ProCLAD for assembly. With the wide variety to choose from, the architects were then able to confidently make their pick and select a color range that was consistent with the original concept.
“After comparing several options, we decided that a range of three colors with a slight variation would best represent a naturally weathered steel, but in an interpretive manner. We selected a range of warm brown tones that are found in weathering steel that has been exposed to the elements over time,” said Eddie Abeyta, HKS principal and commercial design director.
McElroy Metal supplied 40,000 square feet of 18-gauge Galvalume steel coil coated with Valspar’s Classic II Fluropon in a custom color combination of Barrel Brown, Fudge and Mustang.
“It’s a testament to the relationships we have forged in the exterior cladding markets with key suppliers such as U.S. Steel and Valspar as well as visionary exterior cladding contractors like ProClad Inc. The culmination of this project was simply a direct result of teamwork,” said Mark Lawson, VP of sales at McElroy Metal. “Everyone had to be on the same page to achieve the structural and aesthetic goals of HKS, Valspar, ProClad and McElroy Metal. I think this will serve as a signature project for everyone involved.”
Additionally, Win-Con, Inc. supplied the curtain wall, carrying glass across the adjacent sides of the hotel. The Win-Con Unitized curtain wall system included 200,000 square feet of glass with interior mullions and exterior fins coated in Valspar’s Classic II Fluropon in Bright Silver by Bonnell Aluminum.
“With the combination of design flexibility, attention to energy efficiency and superior detail to quality materials, Win-Con’s Unitized curtain wall system complemented the one-of-a kind JW Marriot,” said Charlie Ruyle, VP of Win-Con Enterprises, Inc. “The towering Unitized curtain wall achieved the aesthetic look desired by the design team and allowed for coating customization of the aluminum fins and mullions. Valspar is one of our preferred manufactures due to their range of capabilities so we were thrilled to work with their team to supply the coating for components of the curtain wall.
“We track the external market trends in a number of our global end use markets such as industrial production, commercial construction new builds, transportation builds, electrical motor production and pipeline miles constructed,” said Michael Cash, senior vice president and president, industrial coatings, Axalta Coating Systems. “Our best estimate based on aggregated third party data is that the global industrial coatings end markets grew by three to four percent in 2014. By working closely with our customers, and by welcoming many new customers to the Axalta family in 2014, we were able to grow faster than the overall size of a number of our end use markets last year.”
“The industrial coatings market covers a large and diverse range of segments and applications,” said Shelley J. Bausch, vice president, Global Industrial Coatings, PPG. While growth rates have slowed in some of these segments due to end market reductions (such as heavy duty equipment), others continue to deliver strong growth performance. With PPG’s global capabilities, we have been able to leverage these areas of growth to continue to outpace the market.
“Additionally, as customers continue to look for ways to improve performance and provide new functionality to their end products, new areas of growth are evolving for coatings,” Bausch added. “High performing coatings can be used to meet multiple needs, reducing the need for specific substrates or replacing mechanical solutions.”
Sherwin-Williams has seen growth in several areas, including wood finishing, general finishing, heavy equipment and building products. “One market that we’re particularly excited about is OEM prefinished residential and commercial wood flooring coatings market in which we just announced our participation,” said Nick Bartoszek, global marketing director – liquid and powder products, Sherwin-Williams. “In all of the markets we serve, customers are asking for products that offer low or zero-VOC solutions, as well as ways to improve their finishing processes. We look for ways to become a true partner with our customers, providing expertise that offers guidance well beyond the product.”
According to Klaus Moller, Hempel group vice president of marketing and business development, the general market for industrial coatings grew by approximately three percent between 2013 and 2014. “In general, the industry was boosted by government investment in infrastructure projects, especially in the Middle East and Asia, he said. “We expect the overall industrial coatings market to grow inline with global GDP. We foresee that commercial architecture will show a growth rate above that of the overall market while oil and gas growth rates look more uncertain due to the current low oil and gas prices.”
The industrial coatings market comprises many diverse segments – each offering its own set of opportunities and challenges. “Each application segment presents unique growth opportunities,” said Bausch. “Globally, expansions in oil and gas and transportation of these commodities provide multiple coatings opportunities. Trends in electronic materials and their use beyond computers and mobile phones to automobiles, commercial buildings, and homes provides a diverse growth opportunity for coatings. And as a macro trend, the continued expansion of the transportation market – personal and commercial vehicles – gives a robust opportunity for growth. This is particularly apparent in developing regions.”
“Trends in construction segments are mixed, both geographically and by application segment,” Bausch added. “However, the need for coatings in these segments continues to be robust. And finally, new and increased performance requirements also are driving growth opportunities. As an example, we see tremendous opportunity for growth on frames and chassis in the automotive and transportation segments through their growing demand for improved corrosion resistance. With the continued strength of the automotive sector, this will be positive for industrial coatings.”
Sherwin-Williams is witnessing and responding to growth opportunities across all segments. “For wood finishing, Sherwin-Williams introduced our Ultra-Cure Waterborne UV Topcoats for our wood finishing customers who are looking for flatline finishing technology to help meet regulatory requirements while also increasing productivity,” said Bartoszek. Recently, formaldehyde in wood finishing has also been in the news; we offer a full line of formaldehyde-free lacquers, conversion varnishes, primers and surfacers for manufacturers that wish to address this issue. In some cases, use of these products has helped end users meet LEED certification.”
“In general finishing applications, new resin developments can yield lower VOCs and reduced HAPs in polyurethane coatings, which help finishers meet sustainability goals, save money on energy and equipment, without sacrificing appearance,” added Bartoszek. “Heavy equipment manufacturers typically have firm coating specifications in place, so helping them and their tier suppliers take cost out of the coating process by working with them to gain efficiency continues to be paramount. In building products, architects and specifiers need to meet stringent AAMA 2605-13 specifications for coatings to meet long-lasting performance standards in a variety of weather conditions. As the only U.S. licensee for Arkema Kynar 500 FSF PVD Resin, we think we are in a good position to help them meet those standards, using 100 percent Kynar in our SHER-NA 5000 Fluorosurfactant-free architectural coating. And for the prefinished wood flooring market, we’re offering a new family of prefinish coatings that includes UV-curable wood flooring coating systems.”
Cash said that one of the strengths of Axalta’s industrial business is the global product portfolio it offers which, combined with strong sales teams around the world, can match potential growth distribution in different regions. “This is key because end use segments can grow at different rates in different economic regions,” said Cash. “For example, there’s anticipated growth in drilling, albeit at different rates of growth in different geographies, which provides markets for our Nap-Gard FBE products. Similarly, faster rates of industrialization in China and elsewhere in Asia suggest room for growth in commercial construction and the industrial maintenance market.”
Industrial coatings manufacturers continue to be challenged to meet cost and performance requirements. First and foremost, customers expect their coatings to meet the most stringent performance requirements.
“The coating has to work; that’s a given,” said Bartoszek. “You’re really not in the game if the coating doesn’t meet the customer’s needs. We see our differentiator as the ability to provide expertise and improvement beyond the sale of the product. In some cases, that may actually mean selling less of a coating through process improvements. But helping a customer take costs out of the process through collaboration, or helping them meet sustainability goals, is a worthwhile endeavor. We seek to partner with our customers because we know that if they succeed in all aspects of their finishing process, we’ll be working together for a long time to come.”
“To meet their business demands, they need us to provide coatings that improve corrosion performance, provide additional functionality and support light-weighting or other substrate changes,” said Bausch. “From a cost and efficiency perspective, they need us to provide solutions that accelerate production throughput, enable faster cure times, utilize lower cure temperatures, and reduce process steps. Continual improvement of environmentally friendly coatings represents another key area for increasing performance and delivering our customers a competitive advantage. PPG is pursuing advances in each of these areas, regardless of industry, geography or legislation.”
“Our industrial coating customers are looking for a paint company that will become natural extensions of their business and offer a true understanding for what will help them become successful,” said Cash. “This can happen through superior product performance as well as the technical service and support we provide onsite to help our customers achieve their performance goals. It is one thing to provide superior, innovative products, but it is truly an achievement to help our customers benefit from the full capability of our products in the unique coating application environments of their businesses.”
Customers needs are dependent on the specific application. “Owners and engineering companies typically look for long-term corrosion performance verified according to recognized performance standards, such as ISO or NORSOK,” Moller said. “In addition, specific performance criteria, such as chemical and heat resistance, can play an important role for customers when selecting coatings for more demanding and specialised applications. Fabricators and applicators usually focus on the application properties of the coating, such as drying time, over-coating intervals and surface preparation requirements.”
Moller added that all customers would like to reduce their overall costs. “End users, therefore, look for a longer lifecycle for their investments and a lower total coating cost, including costs associated with application and surface preparation. Many applicators, particularly in shipyards and fabrication factories, can reduce costs by increasing productivity through the use of more surface-tolerant coating systems or faster drying systems. These systems also enable applicators and owners to reduce their carbon footprint. Fast-curing products enable steel fabricators to reduce the energy used to heat drying halls, for example.”
Industrial coatings manufacturers have launched a diverse lineup of products. This year PPG has introduced four new industrial coatings that the company believes represent significant advances in the industrial coatings industry.
“One example is our new VERSABOND pretreatment system,” said Bausch. “This product features a proprietary hypernucleation technology that improves the corrosion resistance of mixed-metal substrates on auto parts and accessories while enabling manufacturers to extend bath life, reduce sludge and lower process temperatures to save energy. By enabling the use of lighter mixed-metal substrates, Versabond pretreatment also supports the broader industry strategy to make vehicles lighter.”
PPG launched ENVIROCRON HTE (high-transfer-efficiency) powder coatings. These products feature a cross-link polymer that enables them to penetrate and apply evenly to metal parts and product assemblies with complex surfaces such as refrigerator racks, patio tables and architectural components.
PPG also launched PERFORMALOC advanced productivity coatings. “These coatings represent an entirely new category of products because they cure fast and hard without baking or forced drying, which makes them ideal for OEMs with limited or no oven-cure capabilities,” added Bausch.
Over the past year Axalta has launched or expanded the global footprint of quite a few products designed for the industrial market and which, in some cases, also serve its large transportation customer base.
“A few examples of the products we have launched in the past year include the global launch of Alesta powder coatings architectural product line and color collection,” said Cash. “The Alesta Global Color Collection is designed to provide assured long-term protection of monumental architectural structures with an innovative color range. We introduced the Alesta ZeroZinc next generation zinc-free anticorrosion powder primers. Our Imron EY High Productivity Basecoat and 8890S Clearcoat system for the commercial vehicle market was added to the Imron family. It is designed to improve throughput and reduce delivery times by allowing for a shorter bake and provide customers with options to meet production demands and save money. Axalta SE6000 Scratch and Mar Resistant Clearcoat was introduced and is designed to provide increased protection within the high use sport vehicle markets where we have a strong position today. The patented dual cure nature of the chemistry allows for faster cure and improved hardness on cool down, to enhance the overall protection while providing premium appearance.”
Sherwin-Williams has several new products that will be introduced throughout the remainder of 2015. Recent new product releases include Powdura OneCure, a two-coat mono-cure system for heavy equipment and general finishing, Ultra-Cure Waterborne UV Topcoats for wood finishing and Prefinish coatings for wood flooring.
Hempel has launched a number of new products recently. AvantGuard technology is a new zinc technology that increases zinc activation to significantly improve the anti-corrosive performance and mechanical strength of the coating without increasing zinc content. Activated zinc products are specially designed for harsh environments. They provide increased corrosion protection and are easy to apply. As a result, they are redefining protection, redefining durability and redefining productivity.
Corrosion under insulation (CUI) is a major challenge and costs process industries significant lost revenue from downtime, repeated maintenance and replacement of corroded parts. “Versiline CUI uses carefully selected barrier pigments to make it highly effective against corrosion under insulation, even under cyclic conditions,” continued Moller. “In addition, its excellent heat-resistant properties make it extremely resistant to micro cracking, even when subjected to extreme temperatures, from cryogenic (-196ºC) up to 650ºC.”
Another new product from Hempel is HEMPACORE intumescent coatings. The product insulates structural steel so it can retain its load-bearing capacity for up to two hours in a fire, giving people valuable time to evacuate.
Hunt Construction, the contractor on the project, reached out to ProCLAD Inc., the metal wall design company it had previously worked with on a JW Marriott in Indianapolis. Representatives from Hunt, ProCLAD and HKS consulted closely to determine if there was an alternative solution that could deliver the appearance of weathered steel at a lower price. The architects wanted dimensional panels with varied colors that would read well from far away, since the panels would be installed on the high-rise portion of the building. Craig Caudill, executive vice president for ProCLAD, suggested using formed Galvalume panels painted in dark, medium and light shades to mimic the appearance of rusted steel. Caudill knew that using a variety of colors of Valspar Fluropon coatings could help create the dimensional variety the architects were looking for. Additionally, the coating would maintain its look for years to come, as Fluropon is known for its durability, exceptional color retention, and resistance to chalking and chemical degradation.
“The hard part started then,” said Caudill. The team liked the idea, but wanted to see a sample before committing, and they needed it fast. ProCLAD contacted Valspar, which was able to color match the three shades, work with Western Extrusion to coat them on steel flat stock, and ship them to ProCLAD in less than two weeks. ProCLAD then wheeled a wall mockup of the sample panels onto the HKS lot.
The architects liked the appearance of the panels as well as the lower cost of the solution, but still weren’t ready to commit to the colors.
“HKS provided us with a few paint samples and requested to see five new sets of colors in varying shades of brown, along with a few metallic options,” said John H. Kelly, metal buildings market manager for Valspar. “Clients typically request one or two color variations, but in this instance, we needed to create nearly 20 color options to ensure the best possible result for the client.”
Rising to the challenge, Valspar’s lab team was able to complete the project between Christmas and New Year’s Day, so ProCLAD was able to show HKS 15 new panel mockups shortly after the New Year. Once the color formulations were created, the lab worked cohesively with the Western Extrusion team to quickly spray the oversized panels and have them shipped to ProCLAD for assembly. With the wide variety to choose from, the architects were then able to confidently make their pick and select a color range that was consistent with the original concept.
“After comparing several options, we decided that a range of three colors with a slight variation would best represent a naturally weathered steel, but in an interpretive manner. We selected a range of warm brown tones that are found in weathering steel that has been exposed to the elements over time,” said Eddie Abeyta, HKS principal and commercial design director.
McElroy Metal supplied 40,000 square feet of 18-gauge Galvalume steel coil coated with Valspar’s Classic II Fluropon in a custom color combination of Barrel Brown, Fudge and Mustang.
“It’s a testament to the relationships we have forged in the exterior cladding markets with key suppliers such as U.S. Steel and Valspar as well as visionary exterior cladding contractors like ProClad Inc. The culmination of this project was simply a direct result of teamwork,” said Mark Lawson, VP of sales at McElroy Metal. “Everyone had to be on the same page to achieve the structural and aesthetic goals of HKS, Valspar, ProClad and McElroy Metal. I think this will serve as a signature project for everyone involved.”
Additionally, Win-Con, Inc. supplied the curtain wall, carrying glass across the adjacent sides of the hotel. The Win-Con Unitized curtain wall system included 200,000 square feet of glass with interior mullions and exterior fins coated in Valspar’s Classic II Fluropon in Bright Silver by Bonnell Aluminum.
“With the combination of design flexibility, attention to energy efficiency and superior detail to quality materials, Win-Con’s Unitized curtain wall system complemented the one-of-a kind JW Marriot,” said Charlie Ruyle, VP of Win-Con Enterprises, Inc. “The towering Unitized curtain wall achieved the aesthetic look desired by the design team and allowed for coating customization of the aluminum fins and mullions. Valspar is one of our preferred manufactures due to their range of capabilities so we were thrilled to work with their team to supply the coating for components of the curtain wall.